FLEXIBLE BARRIERS OPTING
- Monday - 24/06/2024 23:22
- Close page
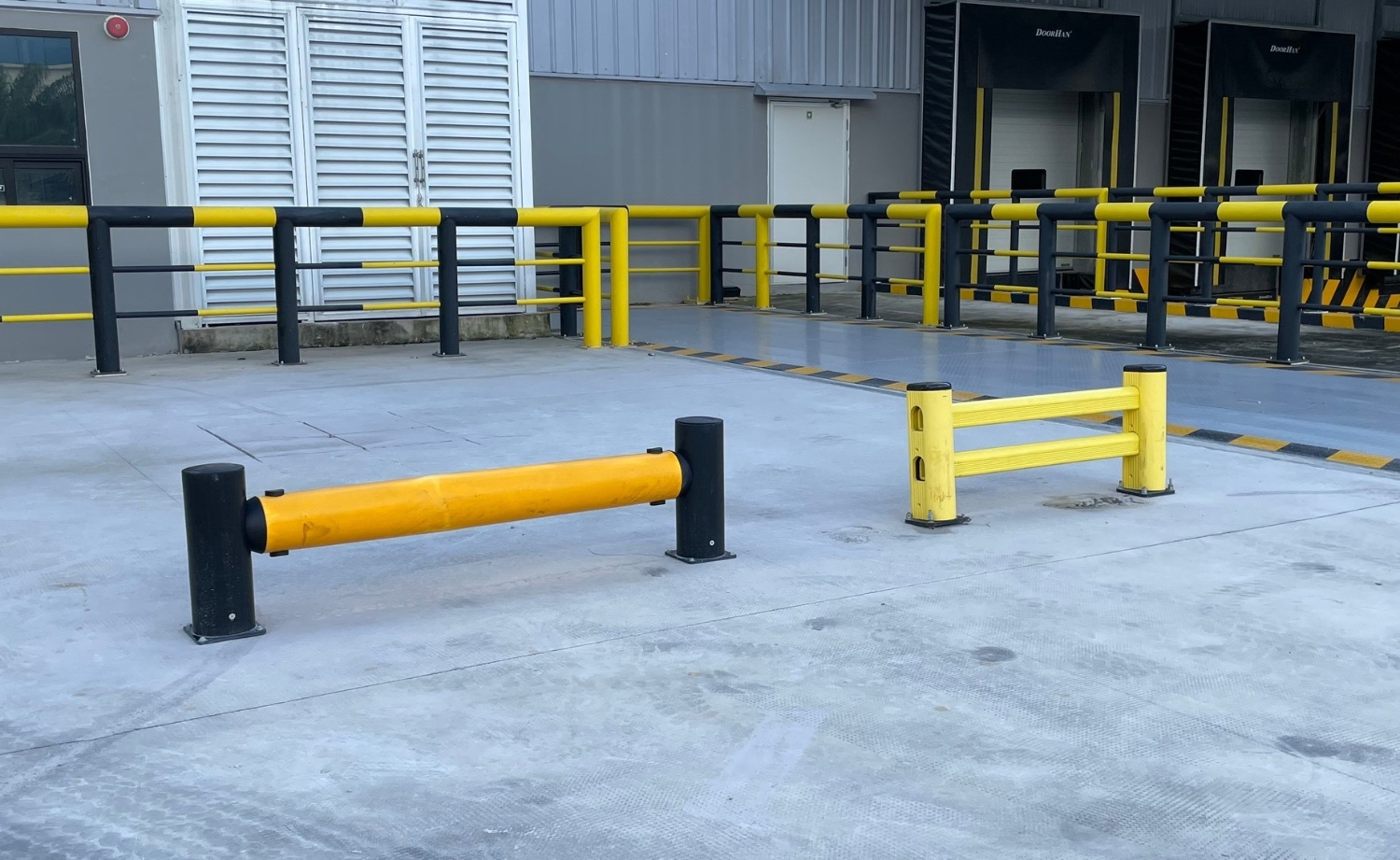
Nowadays, replacing traditional steel barriers with flexible plastic barriers made from synthetic materials has become quite common due to the advantages that they offer. These flexible barriers have several benefits á below:
- Non-Destructive Impact: They do not damage vehicles upon collision.
- Stability: They remain anchored to the concrete surface even after impact.
- Corrosion Resistance: Unlike steel, they do not rust and do not require repainting after prolonged use.
- Easy Maintenance: They are easy to clean.
- Simple Installation: No “hot works” like welding or cutting is needed during installation, making them suitable for areas sensitive to fire or explosions, such as fuel depots, paint factories, and printing ink facilities.
However, when using flexible barriers, it’s essential to consider the material they are made from. Currently, most flexible barriers are constructed using synthetic plastics, primarily PVC (Polyvinyl Chloride) and Polypropylene or HDPE (High-Density Polyethylene).
- PVC: Sturdy, solid, with a dense and homogeneous structure. It exhibits excellent elasticity, returning to its original form after impact. PVC barriers are resistant to scratches, easy to clean, and do not accumulate moisture or dust.
- Polypropylene or HDPE: Porous structure and slightly softer than PVC. It offers good elasticity but is more susceptible to dents and scratches. Polypropylene and HDPE barriers tend to accumulate dust and moisture and can be challenging to clean.
Choose the material that best suits your specific needs when opting for flexible barriers.